Process-based management
All about process-based management in an organization.
Introduction
Any organization or company that creates goods or provides services is directly related to its processes. These are the steps we have to go through to reach a final result. Process-based management presents a new form of internal organization for our business that comes to bring greater flexibility and ability to adapt to the environment, which will allow us to remain competitive in the market.
Below, we will tell you everything you need to know about process-based management, its advantages, application methods, tools that facilitate its exercise, and more.
What will you find on this page?
What is process-based management?
Difference between process and procedure
Difference between process and procedureLeer completo
TABLE OF CONTENTS
Related concepts
What is a process?
In a very general way, we can say that a process is a set of activities that create or modify something. Everything we know is made through a process, whether it is something abstract like a service or something tangible like a good: it includes all the tasks we carry out to reach a result. In general, processes involve several people or teams of people, who work together to achieve the required goal.
Process vs. Procedure
When we speak of a process, we should not confuse it with a procedure. Although they seem the same, it is important that we know the main difference to be clear when we should refer to one or the other. The processes, as we said, are sets of actions or tasks to create or modify something, the procedures are those tasks that we carry out and that are part of the process. The procedures are aimed at meeting specific objectives within the general goals of the process.
What is process mapping?
Process mapping is a management tool used to design the flow of your activities. It is used to graphically represent the processes that are carried out in a company. As its name indicates, it is a conceptual map that aims to easily represent the operation of a company. Some of the advantages of process mapping are:
- It is used as an aid to train workers from all areas on the processes that a company carries out.
- It is a good tool to detect problems. If we are having problems with the result, we can go to the process map to see where in the chain they are making errors and fix them.
- It is very useful for achieving standardization.
- It helps maintain organization and completion of each task.
- It encourages teamwork, making each member collaborate in its creation and once it is done, each one knows what their colleagues are doing.
To carry out a process mapping, there are nine stages that we must put into practice:
1. Determine the objectives: it is important that we define the objectives of each process to determine where our project is headed.
2. Identify the inputs of the process: they are all the elements that are modified in a process. They can be human resources, physical, or data, among others.
3. Identify the customers: customers and the interactions with them during the process.
4. Identify the outputs of the process: they are the deliveries that are made at the end of each process.
5. Identify the components of the process: they are all the inputs and resources that we need to carry out the process.
6. Identify suppliers: they can be internal or external, they are individuals within the company or external suppliers of inputs.
7. Understand the limits of the process: when it starts and when it ends.
8. Document the process: it is recommended to do it in a flow chart.
9. Identify failures to solve them: it is important to determine the effectiveness of the processes. Detecting failures is important to be able to adjust those actions so that next time we don't have problems.
Macro processes | Subprocesses
Macro processes are the processes with a high degree of complexity while subprocesses are the processes with a lower degree of complexity.
In the macro process identification phase, it is important that the institutional function and mission be reflected and that managers validate the work of all areas. There are different types of macro processes that can be identified in a company, such as the strategic, missionary, support. The macro processes group all the processes that have a common objective.
Subprocesses are incorporated once all the other processes have been approved and the stage of evaluating whether it is necessary to incorporate new processes for the fulfillment of the objectives arrives.
Transversal processes
Within the macro processes are the transversal processes; these are the processes that go through different areas of a company and come to break with the schemes of the flow of activities in silos. The organization in silos is one of the most widespread practices although it is one of the least recommended. These types of organizations are characterized by having managers who accumulate information, do not promote the movement of personnel, and avoid pooling resources between areas. The main problem in these types of organizations is that they focus on looking inward instead of expanding outward.
Putting together transversal project teams helps to break with this old way of doing business and makes teams collaborate, share their knowledge, and look to the future to enhance the growth of the company.
Process mining.
Process mining is an analytical discipline to discover and monitor processes as they are and not as we think they should be. It is the way in which more real information is obtained about how the processes are carried out in any organization that we apply it. This technology makes it possible to understand how business processes are used and to detect errors, this is done by extracting information easily stored in the system.
Some of the main advantages of process mining are the following:
- It provides objective information
- It is faster and cheaper than process mapping
- It gives complete visibility to your processes
- It delivers value quickly and easily.
Formalized processes vs. informal processes
Formalizing processes is a complex task that may seem overwhelming at first, but once we start, we can see the advantages of having done so. It is much easier to manage a company with formalized processes than a company that we do not know how it works. In addition, the formalization of the processes gives us a framework of more outstanding professionalism and can help us reach the objectives of our company.
Disadvantages of informal processes
The informality of processes is not an action that is done on purpose, it is generally related to the beginning of companies and the limited ability to detect the changes that must be implemented on time. They are useful to balance the growth of the internal structure of the company at the same time as its sales grow.
Informal processes can work when the company begins to take its first steps; however, once it becomes bigger and begins to incorporate areas and resources, it is essential that its processes be formalized to avoid disorganization and the loss of resources and supplies.
Working with informal processes leads to working with information that has not been corroborated, which can also bring us negative consequences in carrying out the processes and delays. All the inconveniences that arise in our organization will end up directly affecting our service and our relationship with customers since they will not find in us the service that we said we offer. It is for all this that it is always preferable to try to formalize the processes, even if it seems complicated at first.
Optimization of processes
The optimization of processes refers to actions made by the organization to improve productivity, the security of the information, and reduce operating costs. The improvement of processes allows us to rationalize workflows, improve communication, and anticipate changes, among other actions that in the long term will contribute to improving our productivity and competition in the market.
To achieve improvement in your processes, we recommend you take into account these 4 steps that we explain below:
1. The first thing you should do is identify the problematic process that you want to improve. You must define the purposes and goals you want to achieve.
2. You must analyze if the process you want to modify currently meets some of the objectives set at the beginning, if it works for production and if it is useful.
3. Once you have identified and analyzed the improvements you can make, you need to implement the changes
4. The last step you must complete is to monitor. This means tracking the implementation of the process to analyze whether it works as expected and to identify the improvements introduced by the new version.
Root cause analysis
Root cause analysis (RCA) is a method that tries to eliminate problems in a process from its root. It seeks to find the problem and find out what is causing it to eliminate it and prevent it from happening again, acting on the issues that cause it. The root cause analysis allows preventive management to be able to avoid future problems that may arise due to the same cause.
To carry out a root cause analysis there are different methods that we can apply, the main ones are:
1. The 5 whys: it is a method that consists of asking ourselves why something happens. Studies indicate that generally with the question of 5 whys we can reach the objective, although it can vary.
2. Fishbone: it allows us to visually map cause and effect. The problem would be the main part of the diagram and the possible causes are the edges that come off it. Brainstorming is a good technique to apply to identify them.
3. Pareto diagram: this diagram tells us that 80% of the results are caused by 20% of the factors.
4. Tree Diagram: this methodology is used in counting and probability problems. A branch is added for each of the possible causes, accompanied by the probability.
Continuous improvement
Process improvement is the goal of all organizations. Through the constant review of our processes, we can implement actions to achieve continuous improvement and, thus, achieve the desired results.
How can we know if we need to invest in improving our processes? There are some alerts that may be warning us about this that you should pay attention to; these are:
- In the company, there are different people doing the same job.
- It is not defined who is in charge of carrying out each activity.
- The purpose of an activity is not clearly defined.
- You do not know if you have the necessary human resources to carry out a certain activity.
- In the company, you make plans for less than a year.
- You must constantly be doing urgent tasks.
To implement continuous improvement, there are tools that make the process simpler: SixSigma, Lean, and TOC are the three main ones that we will present below.
SixSigma
SixSigma is a methodology that focuses on reducing variability, and reducing or eliminating defects or failures in the delivery of a product or service. To implement this methodology we must follow the following steps:
1. Define: this stage consists of specifying the objective of the problem, or the defect, and validating it.
2. Measure: what we do when measuring is to characterize the processes, identifying the key requirements of the customers, the characteristics of the product, and the parameters that affect the operation of the process.
3. Analyze: in this stage, we intend to find out and confirm the real causes of the problem. An evaluation of data is carried out to achieve this and hypotheses about the possible causes are contrasted.
4. Improve: now, the team determines the relationship between cause and effect to prevent future problems, which allows for improvement and optimization of the process.
5. Control: it is very important to carry out this action to ensure that what has been achieved during the implementation steps works and is maintained for future processes.
Lean
This program consists of a continuous improvement methodology for efficiency in manufacturing processes or service provision. To achieve this, it is based on the suppression of everything that does not add value, allowing work to be done more efficiently and consuming fewer resources. An important factor in this methodology is to take into account the TaktTime: the time between the start of production of one unit and the start of production of the next, which would be the time we need to meet the demands of the customers.
TOC
The theory of constraints aims to intervene in the bottlenecks that limit the capacity of production processes. This continuous improvement methodology aims for companies to generate profits through three indicators:
- process output vs process input
- the cost of stored materials
- expenses associated with transforming inventory
As we can see, continuous improvement is a process that we must do in small steps, it needs the contribution of the entire workforce and it must be communicated in the best way to achieve unification in the implementation of changes. You must be able to find the answer to what is working, what is not working correctly, and what needs to be replaced urgently so as not to have more losses. Once these questions are answered, you can begin to organize the ideal process map and implement the necessary tools and methodologies to optimize it.
To implement the continuous improvement of processes, we need the help of software that allows us to do so. You should take into account the following characteristics when choosing the right tool for your company:
- Automation capability
- Document management capacity
- Ability to collaborate between users
- Data analysis capacity
- Accessibility from any device
Have you ever wondered how continuous process improvement impacts the profitability of your company? Due to the impact process improvement has on our business, profitability is fully involved. For all the improvements that this process implies in our processes, the efficiency that it generates in carrying out tasks, optimization of time, and reduction of the margin of error in future processes, profitability increases considerably by reducing costs when we implement improvements in our production system.
Digitization of processes
Technology invades our lives in all the areas that we know, it is very important to be able to be present in the market and it is a very useful tool to be able to innovate.
The digitization of processes is a step that we must take in our company if we have not already done so. It will bring us numerous advantages such as:
- Agility in management
- Possibility of having the information continuously updated
- Security in our information and documentation
- Simple accessibility to the information that each team needs to work
- It improves communication between the members of each team and the entire company.
To achieve digitization in our processes, we can use certain tools that we will find on the internet; below, we mention some for you to take into account.
It is a web application that allows the creation of diagrams. It is free and you can use it from your desktop.
It is an online collaborative mind mapping, concept mapping, and idea organization software. It has a free version and a paid version where it offers more features.
It is an agile process platform that allows you to connect people, applications, devices, and information to provide an engaging experience.
Process reengineering
In business terms, process reengineering aims to increase management capacity. The time it takes us to reorganize processes is not standardized, as it depends on each company and what kind of tasks need to be re-implemented or reconfigured.
It is important to make a restructuring plan to determine at that moment, the steps that we are going to follow and the time that it will take us to do it, as well as the necessary resources.
The steps to implement process reengineering are:
1. Discovery: the company observes its processes and the environment in which it operates and proposes a strategy to modify the processes that need it.
2. Redesign: detail, plan, and map how the adapted process would work and how it would be implemented.
3. Execution: it is carried out and implemented to achieve the pre-established objectives.
The advantages of implementing process reengineering are:
- Simplification of operation flows
- Time optimization
- Elimination of activities without added value
- Improvement of service quality
- Definition of a new organic-functional structure aligned with the vision of the company
- Definition of a structure for the technological platform adapted to the processes.
Process indicators
Process indicators, or KPIs, are vital elements for companies that are managed by processes. The more detailed the indicators are defined, the lower the risk of encountering erroneous information.
The indicators must always be representative, sensitive to analysis, reliable, and relative in time.
There are different types of indicators; below, we will mention some of them:
Efficiency indicators
These are the indicators that measure the degree of success of the activities carried out with the objectives that were set. There is more efficiency the closer we are to meeting the objectives.
Efficacy indicators
Efficiency has to do with the proper use of resources.
Productivity indicators
Productivity indicators are used to measure the evolution of a process, and determine if each phase to carry it out is consistent. There is also evaluation, which is similar but more specific.
Compliance indicators
In this case, what is measured is whether the processes were fulfilled or not.
Quality indicators
Quality indicators are used to measure whether our customers' expectations were met; whether or not it meets their needs.
Customer service
This indicator is important, similar to quality; it values the product or service obtained by the customer.
For any company, it is important for each task to be monitored, and an indicator to be applied, so that we can have a more detailed record of the objectives we want to meet and whether the established steps are being fulfilled.
As we can see, there are different types of indicators, we must choose the most appropriate to measure each process that we need, they will not necessarily be the same for all companies.
The future of processes
Having made a review of the processes, understanding how they work and their purpose in a company, we can guess what the processes will be like in the future. What we are almost sure of is that they will aspire to automation and integration, two issues that we can already identify in this sector today but that in the future will be much simpler and more common to see.
When thinking about automation, fears and doubts arise about robotic work and the work of human resources. Many times, the fear comes from thinking about what humans are going to work on if machines can do all the work. In this case, we emphasize that this will be an advantage for human resources since companies will be able to use them for tasks that require the human capacity for empathy and creativity. In addition, people will be needed to program the machines, so we do not believe that the technology implemented in companies is going to be harmful to workers, but rather the opposite.
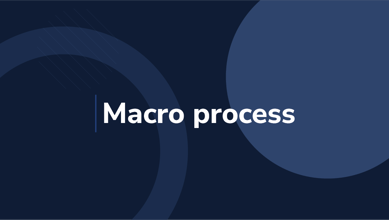
What is a macro process?
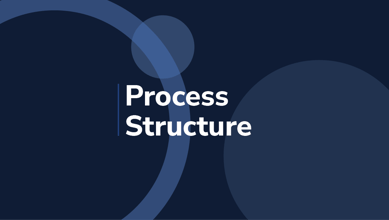
Process structure
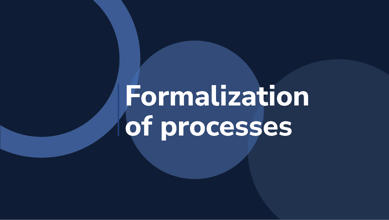
Formalization of processes
Evolution of process-based management.
Advantages of process-based management.
-
It provides a global vision of the operation of the company.
-
It provides more flexibility than an organization based on hierarchies.
-
It favors interpersonal relationships.
-
All the people in the company see themselves reflected in the processes, they know their role and their contribution.
-
It promotes teamwork
-
Processes can be measured, through objectives and metrics.
-
It is possible to know customer satisfaction through measurement metrics.
-
It promotes continuous improvement in the organization. Errors are detected more easily and improvements are implemented.
Processes are the main asset in the scalability of a company.
Process- based management into organizations
Business scalability
Scalability is the ability of businesses to grow, replicate their business model and thus be able to cover more of the market. The key for a business to be scalable is to have processes that work correctly and are implemented as they should be, without wasting material or economic resources and without wasting the skills of our human resources.
Tools for process-based management.
-
Revenue growth
-
Cost reductions
-
It allows risk control
-
It speeds up innovation
-
It improves productivity
Problems in process-based management.
Whenever we implement changes and novelties in any of the processes in which we are used to working, problems and challenges will arise that we must be aware of to improve. Having an outdated process without adaptability to the context where it is applied is a problem that generates unnecessary risks. We must look for updated and accessible technology, which will allow us to save time and resources. We must also take into account getting software that has the possibility of simple integration with others and that is expandable since it is very likely that we will need it in the future
Delves into the relationship between process-based management and business
What do we do in Drew?
We believe that clear processes, supported by the right technology, create an environment where people work happier, and thus make your company more productive.Supplementary material
Resources and editorial content
Practical resources on the main challenges and solutions that every company has.
Process-based management sessions
Meetings dedicated to particularize different problems that transit the current organizations.
Conclusion