Quality
What is it, which are its main functions and challenges, etc.
Introduction
What will you find on this page?
Definition of the Area of Quality
What is the Burndown chart?
What is the Burndown chart?Leer completo
TABLE OF CONTENTS
Related concepts
At this point, we need to clarify what specialists mean when they talk about "Total Quality".
As a perspective or paradigm, Total Quality focuses on to cooperate and participate in every area of the company by gathering information, resources and human capital with a particular goal: obtaining a product with real characteristics adapted to the exact need of the customer.
It is important to mention that quality control is not carried out just by one area or to a particular product, but it acts in an interactive way among every member of the company. It acts from the design, production and delivery of the product to the after-sale guarantee, support and constant predisposition to customer experience.
As we previously stated, the Japanese management model meant a very important point in quality evolution since they were the ones who focused on the customer, not on the product. It penetrated into markets in the 1970s and its system expanded until it became the prevailing system at present, which means that it does not matter if a product is perfect, it will not be useful if it does not satisfy customers.
Understanding their wishes, relating with them, working towards fulfilling their needs and accompanying them throughout the process (including after-sales) are the goals of every competent company. This way, we can understand customers according to "Karl Albert's Principles" in the following way: the customer is the most important person for the business; he/she never depends on the company but the other way around (the company depends on him/her); he/she is not just a number or a potential sale, but a being with needs, tastes and preferences we need to fulfill: that is the goal.
That is why some areas have emerged that must be part of a company because they provide reliability and commitment, such as "Customer Service", "Contact" and "After-sales Guarantee".
Delve deeper into our
Business Concepts
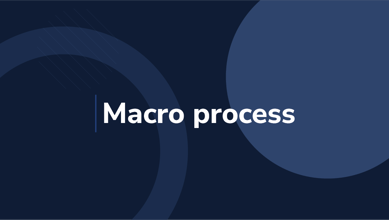
What is a macro process?
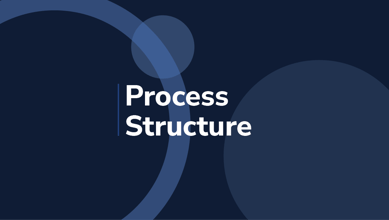
Process structure
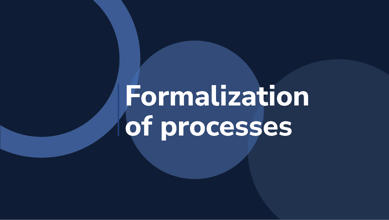
Formalization of processes
A short history of its conception and development over time
-
Handcrafted production stage: from Ancient History until the beginning of the Middle Ages, handcrafted production assured the customer that the final product would be unique because each product was made differently, customized, without taking into account costs and delay in the process.
-
Industrial Revolution: mass production was very important for the growth of nations so in this stage, workers produce a great number of goods without taking into account their quality, since satisfying the demand was their drive. It is characterized by a great exodus of independent workers that were now part of the corporate sector of the first companies.
-
World Wars: these wars meant a milestone in the evolution of quality because the empirical control system turned into an almost scientific system. The important countries financed academic sectors so that they work in their favor by developing highly refined arms. Identifying faulty products was vital to assure a positive outcome. The focus is on the technical conditions of the product and on assuring its availability in case they are needed. Here we can find a quality inspector for the first time.
-
Posguerra: the tragic results of World War I and World War II made it imperative to produce massively and at high speed to alleviate them. The demand for goods was very high and some countries positioned themselves strategically to make their economies grow.
-
Japanese revolution: Japan also was affected after the Wars so it changed its paradigm in order to avoid the detection of faulty products and to focus on assuring the production of goods without flaws. The reduction of costs by preventive controls was part of its strategy. It looked for having satisfied customers and, at the same time, rising above its competitors in terms of quality. Its goal was clear: producing at a low cost, quickly and correctly.
-
The 1970s: based on the goals of the Japanese revolution, the 70s were focused on the implementation of internal processes to assure a better quality of products. The production flow and crosswise control became the main allies of companies. At this point, software and technologies at the service of customers emerged and the first companies that used them gained a great economic advantage.
-
The 1990s: quality control becomes a must in every area of a company, not just in terms of products or services but also in the whole functioning of the company. Inspectors and managers of different areas focused on achieving effective communication among all the areas so that there were no internal errors. The first quality certificate emerged and globalization standardized control requirements for certain areas.
-
At present: nowadays, companies are characterized by the training of quality specialists for each area and a preventive approach instead of corrective actions; present time is highly influenced by software devoted to strengthening processes. Now, it is very important to reduce costs, have a satisfied customer and the concepts of "total quality" and "process re-engineering". At present, companies divide processes by departments or areas; quality managers divide tasks and responsibilities; tasks that do not add value are reduced and the company is seen as a strategic business unit. Now, we can find after-sales guarantees, subcontractors and outsourcing of satellite activities by specialized people that are not part of the company.
Functions of the Quality Area
-
Constant participation in the production process, design, and manufacture of products; also, provide solutions and advice so that you can constantly surpass your customers' expectations.
-
Assessment of the documents related to the quality processes according to the current legal framework. In some activities, minimum quality standards are not optional but they should assure a minimum quality before introducing the product in the market.
-
Leading days of training and improvement of the staff. This way, employees will be trained to foresee any problem before having to solve it. Sanitation prevention is a very important part on which correct quality management relies on.
-
Matching the structure with the requirements of the sector, so if you have to apply the ISO 9001 standards to an activity of the company, you can adapt the activity to the framework of these standards.
- Working crosswise in every area. No matter if the company is small or big, the quality area must intervene constantly in the rest of the teams so that it can make sure that the result of the process is spectacular by auditing, monitoring, and testing the product.
- Optimizing costs, time and resources. Currently accompanied by specific software, it can automate processes in order to eliminate human errors and maximize the profitability of the company.
- Risk management. By changing the approach and adopting a strategy based on taking risks, you can take preventive measures that will have a greater impact on the process.
- Leading the innovation in projects. It is widely known that for a company to keep itself competent and aspiring to success it should be innovating constantly by offering customers a new solution for their needs or a more efficient way of satisfying them; to do this, the quality area must be in a continuous search for change.
Meet the highest standards, ensuring customer satisfaction
Quality in organizations
Quality control in small, medium and large-sized companies
-
Small-sized companies: in these companies, it is possible that one person or a small group of people can oversee the quality of production. It will also depend on the sector of the company because it is not the same to sell shoes or food and to sell medicines or medical supplies; each sector will have its own internal regulations. The quality manager of a small company will be in charge of: maintaining excellent quality in the products, managing and guiding innovation, adapting tasks to the regulations of standards such as ISO 9001, designing processes according to the abilities of the workers and coordinating the way in which they work.
- Medium-sized companies: they have between 100 and 1000 employees and they follow quality patterns more standardized and homogenous than the other types of companies. This way, the area should: document the information and adapt it to current legal frameworks, and evaluate risks and adapt the company to environmental management parameters. Constant training and dialogue flow must be the goals of the area in these companies.
- Big-sized companies: they have over 1000 employees and more than one branch, for sure. This type of company will have to devote quality subdepartments to accompany every area. Work can be stipulated so that communication is efficient to keep the quality of the product. It is usual to find different layers of quality control: a team made up of quality directors, managers and auditors, people specialized in training and innovation, legal and tax regulations experts, etc. When the amount of sales is large, the margin of error that can harm the brand is greater; therefore, keeping the quality level is imperative, not just for not decreasing the sales but also to maintain the good name of the brand
Seven principles of Quality Management
according to current information and not on improvisations, maintaining good relationships to mutually benefit from it, implementing processes by automation or by using software, leadership through managers, delegating tasks, developing new methods and solving problems, and, finally, focusing on continuous improvement so that crosswise standards are assured
New challenges for SMEs in terms of quality
In the previous sections, we learned that companies should update constantly to technological changes, fashions and the new "needs" of their customers, no matter their sales ability. This modern commercial management approach is widely applicable to SMEs because they are the economic drivers and the most exposed companies to the volatility of markets and the economy, so these companies should adopt the so-called "Total Quality" model to survive
Delves into the relationship between Quality and business
What do we do in Drew?
We believe that clear processes, supported by the right technology, create an environment where people work happier, and thus make your company more productive.Supplementary material
Resources and editorial content
Practical resources on the main challenges and solutions that every company has.
Quality sessions
Meetings dedicated to particularize different problems that transit the current organizations.