Production / Operations
Everything you need to know about the production/operations area.
Introduction
What will you find on this page?
Definition of the Production and Operations area
- Efficiency: the way of taking advantage of the available resources.
- Productivity: how to increase the number of deliverables with the same efforts.
- Cost/benefit: the quantification of the real cost of the final product and the obtained qualities.
- Quality: the constant search for improving the deliverable, no matter if it is a product or a service, by working constantly on the flaws so that they are avoided in the future.
What is a process map?
What is a process map?Leer completo
Delve deeper into our
Business Concepts
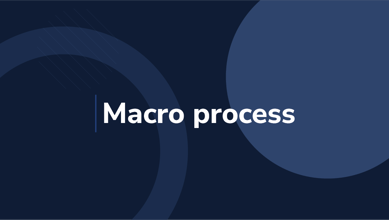
What is a macro process?
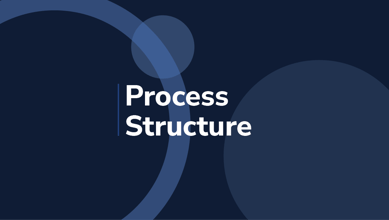
Process structure
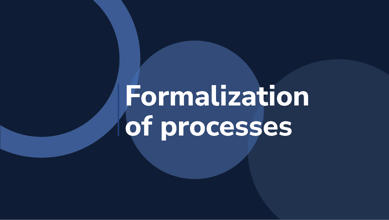
Formalization of processes
A short history of the area and its evolution over time
Following Smith's footsteps, Ford modernized his theory by establishing the assembly line and creating the new theory of Fordism. It can also be said that the French engineer Henry Fayol made important contributions to the ideas of the time by publishing his "14 principles of management".
-
“Total Quality”, developed in 1980 by Dr. Deming, it focuses on the improvement of processes through a cross-wise commitment between managers and workers.
-
"Process Re-engineering", this practice that developed during the 1990s, states that, apart from looking for the constant improvement of processes, its result will always be the same. That is why it suggests the complete study of processes and their (re)design from scratch taking into account the current globalization and market.
-
“Smart Organizations”, emerged from the idea that the current world is in constant change and its needs are specific. Through the study of the five basic abilities that regulate human behavior, they train workers and managers to accept changes positively. These five abilities are: Systemic Thinking, Team Learning, Personal Mastery, Shared Vision, and Mental Models.
-
“Bench Marketing”, a model also developed in the 1990s, suggests studying the processes from the most successful companies and, based on the gathered information, adapting them to troubled companies or companies that cannot solve their internal problems.
-
“Supply Chain Management”, this theory is focused on the efficiency and effectiveness of processes and tries to make all workers from the supply chain contribute to improving costs and results by optimizing transport costs, storage, distribution and the final launching of the product in the market.
-
“Reverse logistics”, also called "green logistics", emerged in the 2000s, and seeks to implement the use of recycled or recyclable resources in all processes so that they have a low impact on the global ecology and the useless materials can be correctly discarded. It is based on the idea of "value recovery"
Functions of the Production/Operations Area
The value of the product is in the production
Production/Operations in organozations
Tasks of the Production and Operation Managers
-
Initial idea: through different methods, it seeks to get into the customers' heads to understand what they need, why they need it and how much they can pay to get it. Once this is assessed, you will choose better.
-
Selection of the product/service:through the analysis of the market and the feasibility, the main characteristics of the deliverable are chosen.
-
Initial design: design options are assessed and the most adequate one is chosen. Managers will take into account its reliability, lifetime, final price, manufacture, time, etc.
-
Final design: by using a film editing studio, you can test the final design. Simulation is a widely used strategy to establish the final specifications and the manufacture diagram. In this stage, you can also assess the development possibilities based on the available infrastructure.
-
Process selection: At this stage, you choose the equipment, the workers, flows, etc. through the monitoring of available technologies and more efficient methods; you can also program work through its planning.
Life cycle of the product or service
-
Development: here is where the business idea is researched previously to its massive production and launching. The first estimations of market reception are made.
-
Introduction: once the product is launched, this area tries to accomplish the biggest impact and penetration in the market by using marketing strategies. In general, price policies choose to sacrifice profit at first to assure customers in the future. Utilities are usually low or non-existent because of advertising and distribution expenses.
-
Growth: positioning the product in the market. Utilities are increasing but they are still low for their potential. Sales rise as prices decline to consolidate their customers.
-
Maturity: the sales increase reduces but customer loyalty rises. The participation in the market is excellent and the company has high profitability. Points of sale are increased.
-
Decline: Period of closure. Sales drop and consumers look for something new. The advertising and the distribution channels reduce and you have to make the decision of taking the product out of the market and start the cycle again with a renewed idea.
Delves into the relationship between administration and business
What do we do in Drew?
We believe that clear processes, supported by the right technology, create an environment where people work happier, and thus make your company more productive.Supplementary material
Resources and editorial content
Practical resources on the main challenges and solutions that every company has.
Production/ Operations sessions
Meetings dedicated to particularize different problems that transit the current organizations.
Conclusion
To conclude, even though it may seem like the Production and Operations area is the core of a company, we do not have to forget that they work in cooperation with the rest of the areas to assure an excellent final product; the contributions that the Human Resources area makes in the training of the staff, Quality in the constant improvement and testing, and Marketing in the market insertion will be vital for the final result.
The automation tools and technology have redesigned the way in which these areas work drastically; by being in constant evolution, it will be the job of a hard-working manager to take this area to the vanguard and with the most favorable working conditions for the business.